PRECISION DIE CUTTING
With over 50 years of expertise in providing customers with innovative die cut solutions, PLITEK® has remained the leader in precision die cutting and narrow web converting of films, foams, adhesive tapes, and other thin gauge materials. The die cutting manufacturing process entails utilizing specialized equipment and tools to convert stock material by slitting, cutting, laminating, forming, and sealing it into custom shapes and designs.
Utilizing our state-of-the-art equipment, we work collaboratively and confidentially with our customers through all stages of their product life cycle from product development and prototyping to high volume production and fulfillment. Extensive die cutting capabilities enable us to produce precision components from a range of materials for a variety of applications. Die cut components can be supplied as pieces, sheets, or rolls.
Capabilities
- ISO Class 8 clean rooms
- Die-cutting
- Kiss cutting
- Slitting
- Multi-layer laminating
- Automated slug removal
- Perforating
- Sheeting
- Scoring/Bending/Forming
- Folding (2-ply, 4-ply W)
- Web cleaning
- Cold forming
- Cold and heat sealing
- Island placement
- In-line vision inspection
- In-line laser cutting
- Tooling (Medical grade, steel rule, machine cavity punch, chemically etched, combination)
Die Cut component materials
ROTARY DIE CUTTING
Rotary die cutting is the process of cutting or perforating a desired shape out of a single or multi-layer flexible material using rotary die cutting equipment and tooling. During the process, a continuous web of material is fed through the rotary press though the nip rollers to a cylindrical die that cuts, perforates, or creases the film. Tight tolerance capabilities, sensor registration, and in-line vision inspection make rotary die cutting ideal for cutting intricate parts with multiple layers. Our equipment has been optimized to allow for efficient dispensing of the finished die cut parts. High processing speed makes it ideal solution for high volume production. Rotary die cut components can be supplied in a variety of peel tab options such as slit liners, folded liners, peel tabs, extended liners, perforations, and creases.
Our equipment allows for multiple material lamination, slitting, sheeting, and in-line cutting registration making it an efficient solution for high volume and quick turnaround production.
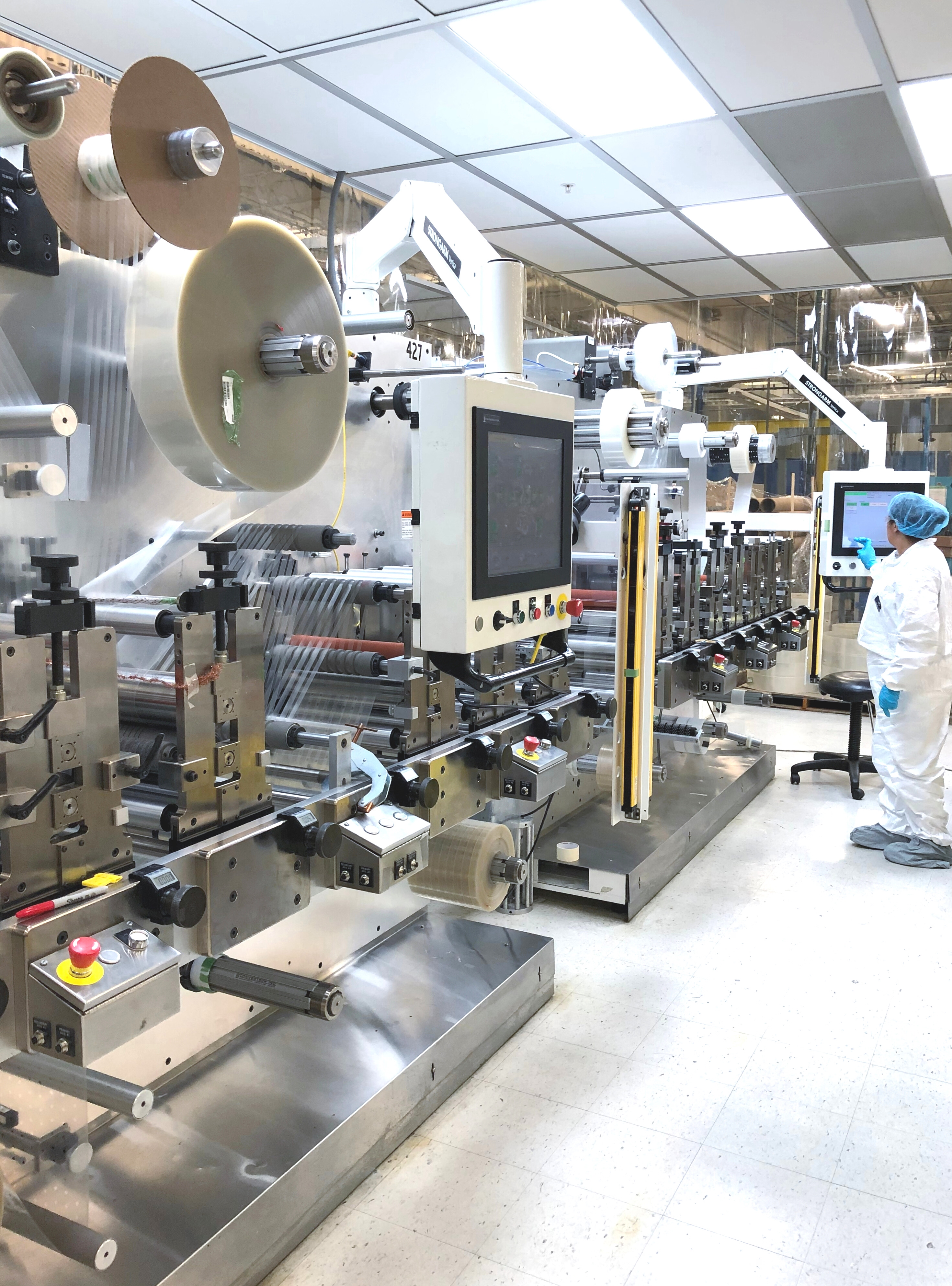

FLATBED DIE CUTTING
Also referred to as steel rule die cutting, flatbed die cutting is a type of die cutting that cuts the stock material by pressing a sharp steel rule die into the material against a flat surface stamping out shapes. This die cutting method allows for good tolerance capabilities by precisely stamping shapes out of films, foams, and adhesives. The advantages of steel rule die cutting include precision accuracy, low tooling costs, shorter tooling lead time and the ability to die cut thicker materials. Tooling can be designed with medical die board materials for clean room production.
Parts can be provided in roll, sheet, or piece form with a variety of peel tab options such as slit liners, folded liners, peel tabs, or extended liners.
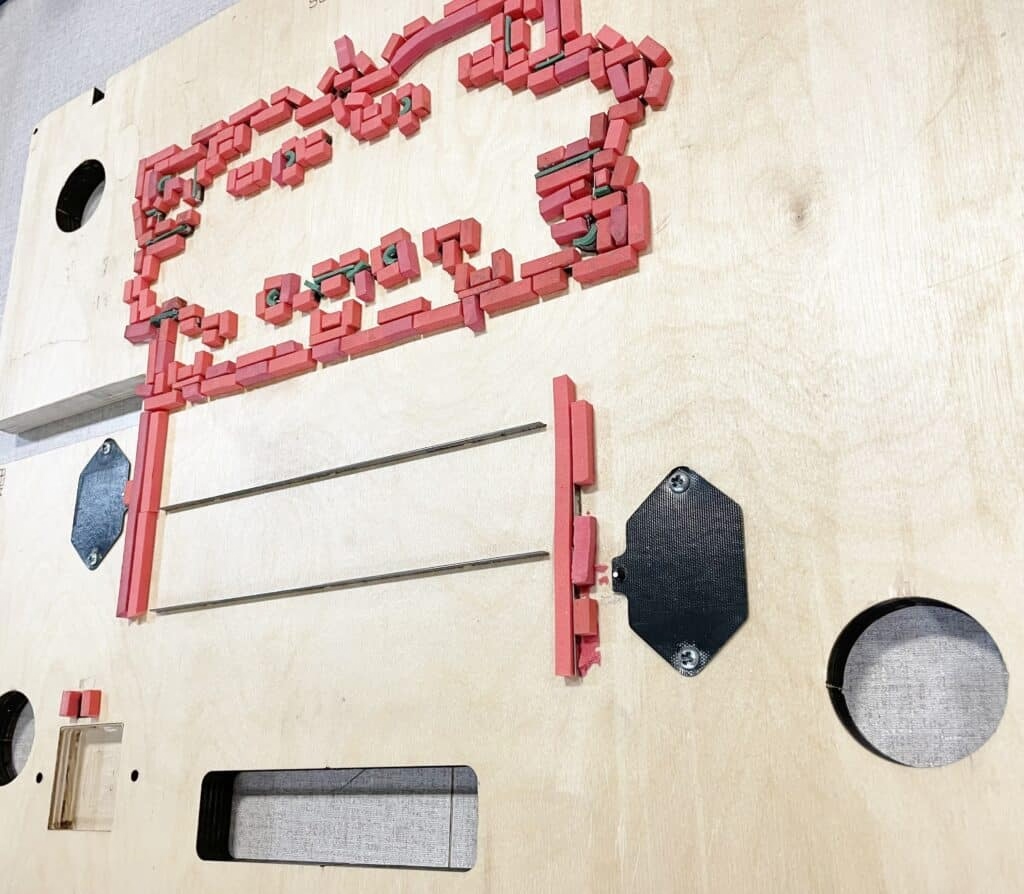
Explore our converting capabilities:
Explore Our Converting Solutions
Learn how we’ve helped our customers with a wide range of converting solutions
PLITEK® is an ISO 9001:2015 and ISO 13485:2016 certified global converting leader.