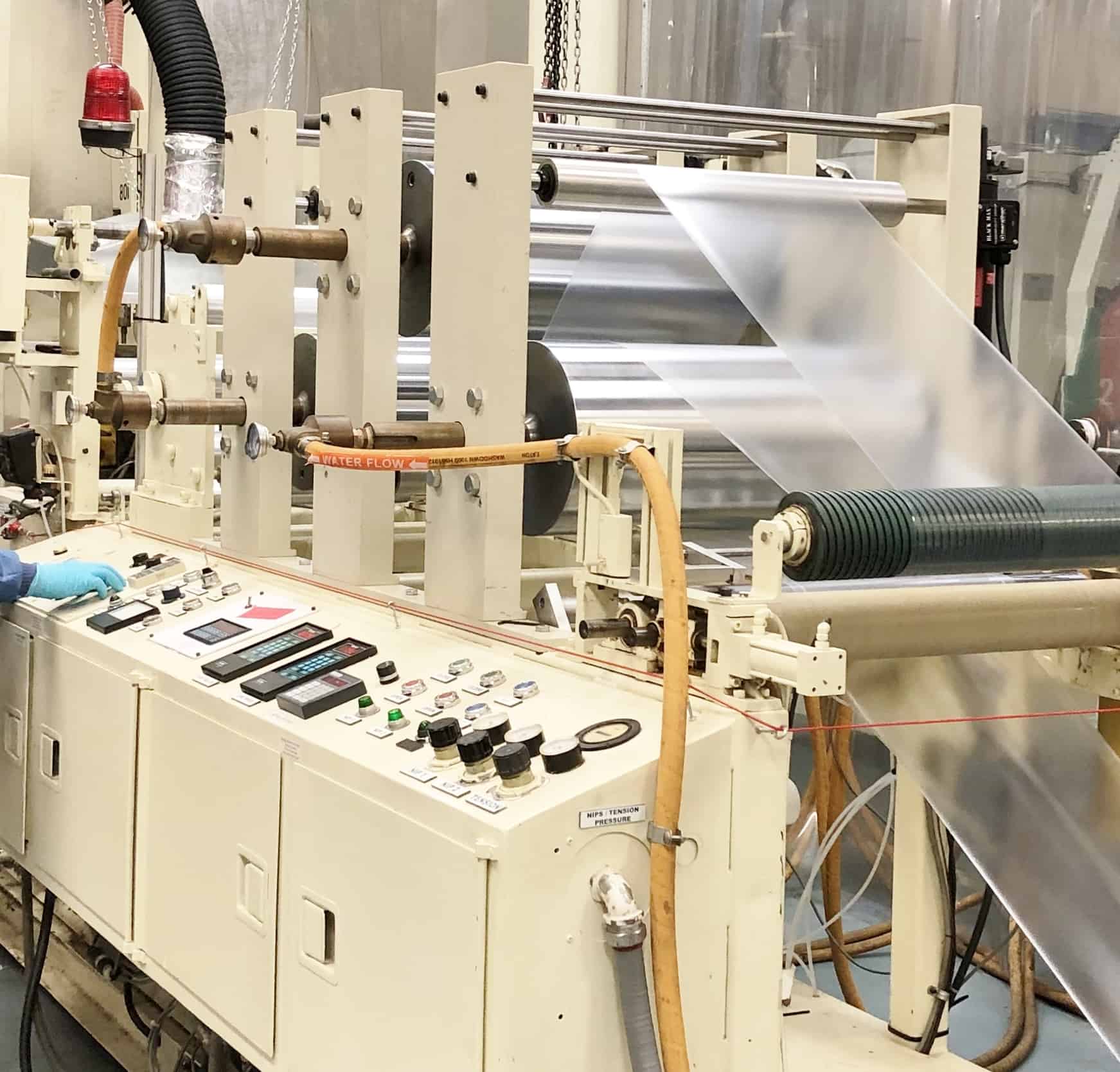
Clean Room Film Extrusion
PLITEK® is a leading contract manufacturer specializing in extruding custom medical grade films in ISO Class 8 clean rooms. We have the ability to extrude smaller startup quantities supporting our customers from a design and development phase, through high volume production and commercialization. Custom films can be provided in roll form, sheet form, or as precision die cut components tailored to meet specific application requirements.
As part of our continual vertical integration, we are in the process of adding new extruding capabilities: co-extrusion and polypropylene meltblown filter media extrusion.
Medical film extrusion is a technology commonly used to make plastic medical grade films. The high-volume manufacturing process involves extruding molten polymer through a slot or die to form a film. Films are strategically produced by propelling copolymers into a steel die at high processing temperatures to obtain the sought-after outcome in flexibility, resilience, and transparency. Strength, barrier, and weight are properties that can be achieved through customization. This offers a great benefit to a multitude of industries including medical, ostomy, wound care, packaging, consumer products, and wearables. Our in-line process allows for slitting of the extruded film as well as lamination of protective film.

Custom EXTRUDED FILMS
- Ethylene Vinyl Acetate (EVA)
- High Density Polyethylene (HDPE)
- Low Density Polyethylene (LDPE)
- Polypropylene (PP)
- Polystyrene (PS)
- Polyester (A-PET, RPET, PET-G)
- Hytrel thermoplastic polyester elastomer
- Santoprene
- Custom polymers
CAPABILITIES
- ISO Class 8 clean rooms
- Cast extrusion
- Sheet extrusion
- Engineered resins
- Multiple resin blends
- Custom color and tints
- Single layer
- Lamination of carrier film
- Varying finish options (smooth, taffeta, matte, other)
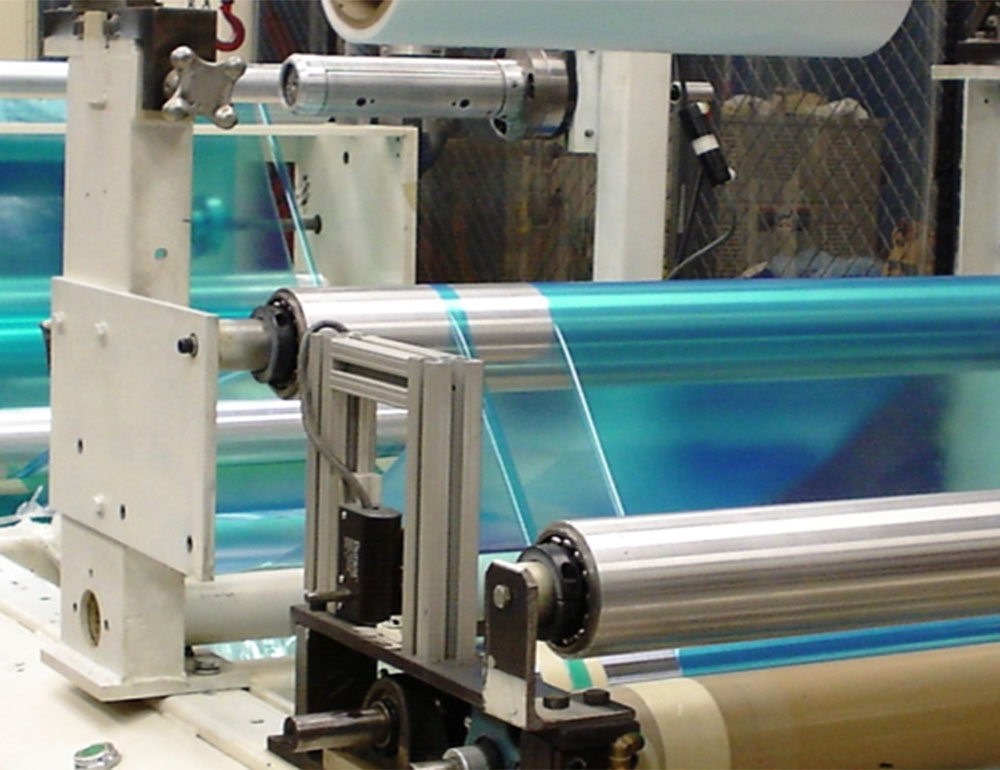
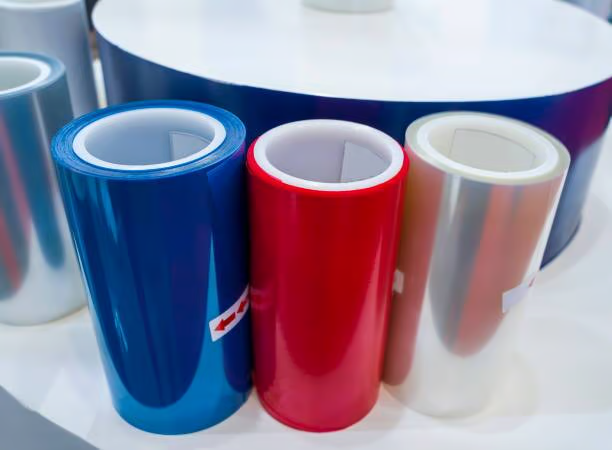
Film Extrusion Methods
Cast Extrusion Process
The cast film extrusion process begins with plastic resin being delivered to computerized extruder equipment. The polymer materials are melted, mixed, and flow into the die system to create a homogenous melt. After progressing through the die, the molten plastic is chilled to form the film and later the edges are trimmed for the final product to be wound onto rolls.
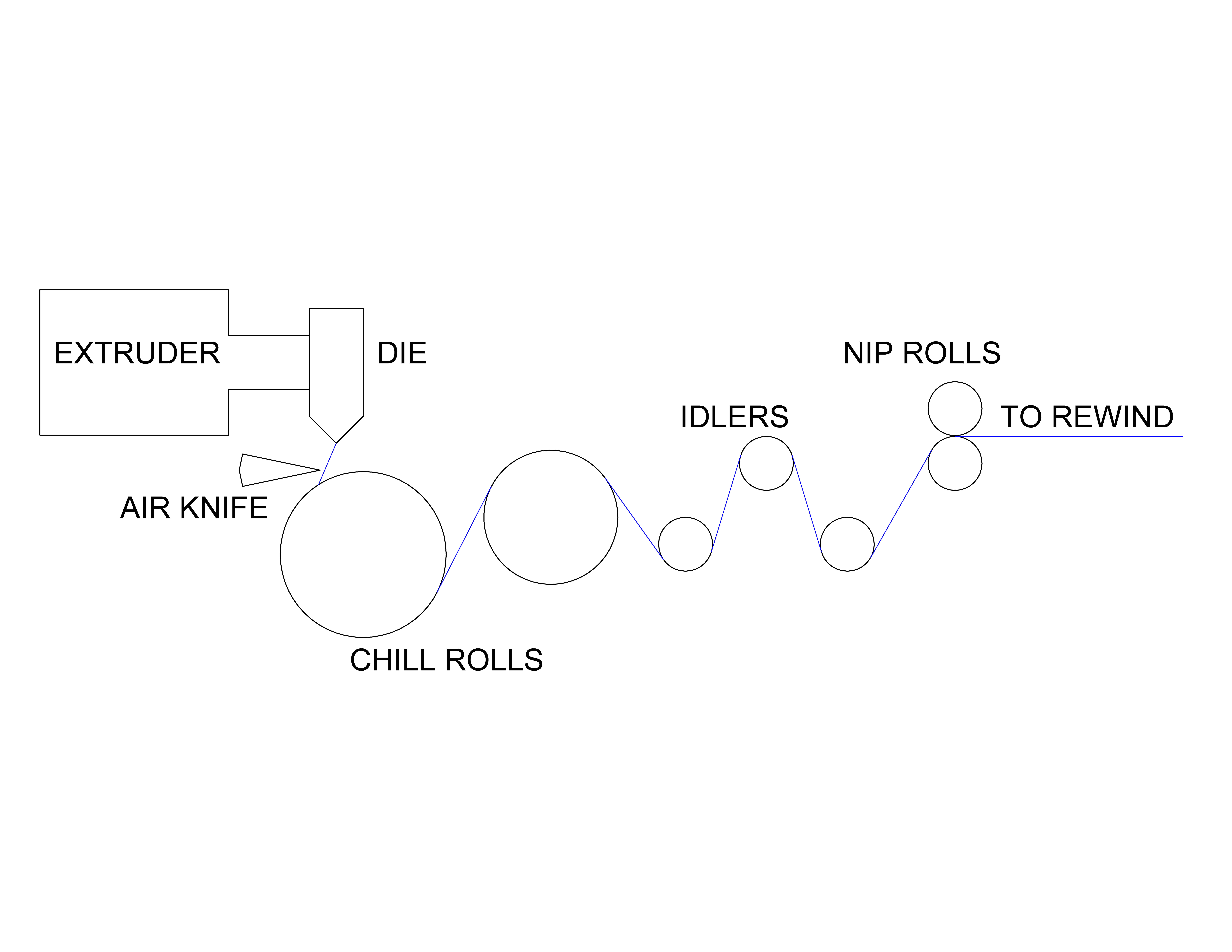
Sheet Extrusion Process
The continuous production process of sheet extrusion occurs with pellets being driven from a feed hopper. The molten flows into a die and is pushed outwards along die lips to produce a molten sheet. After the sheet passes through cooling rollers, it is prepared to have the edge trimmed, and slit to the final required length for the application.
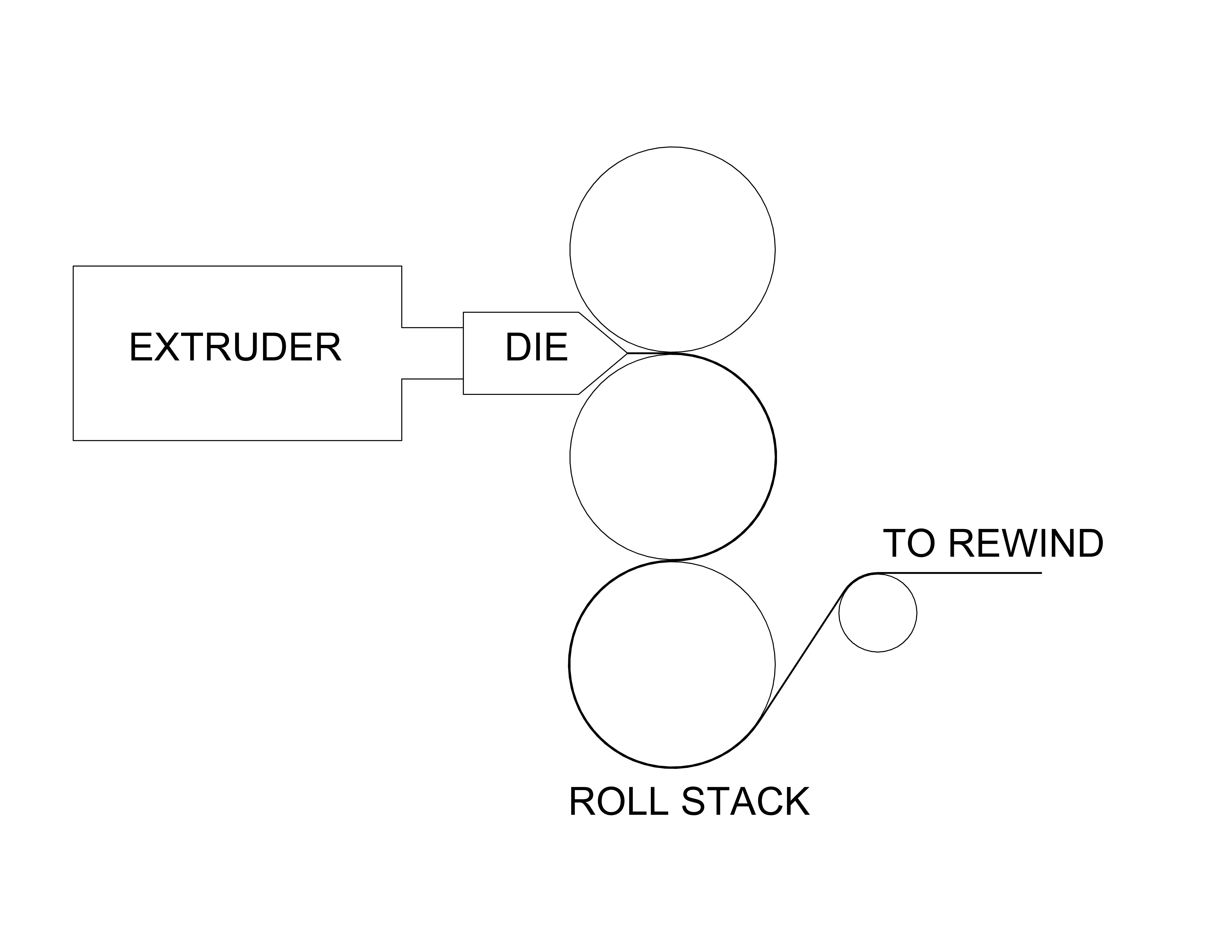
Custom Extruded Film Process
We have the ability to blend multiple resins to formulate custom-made films required for specific designs. Cast or sheet extrusion methods are used in the creation of these engineered films.
COMING SOON
Co-Extrusion Process
A process similar to cast film extrusion. The difference is the ability of forming a single film structure from more than one type of thermoplastic resin. The intention is to produce a mono film structure where each layer contributes a key property that improves the films overall performance.
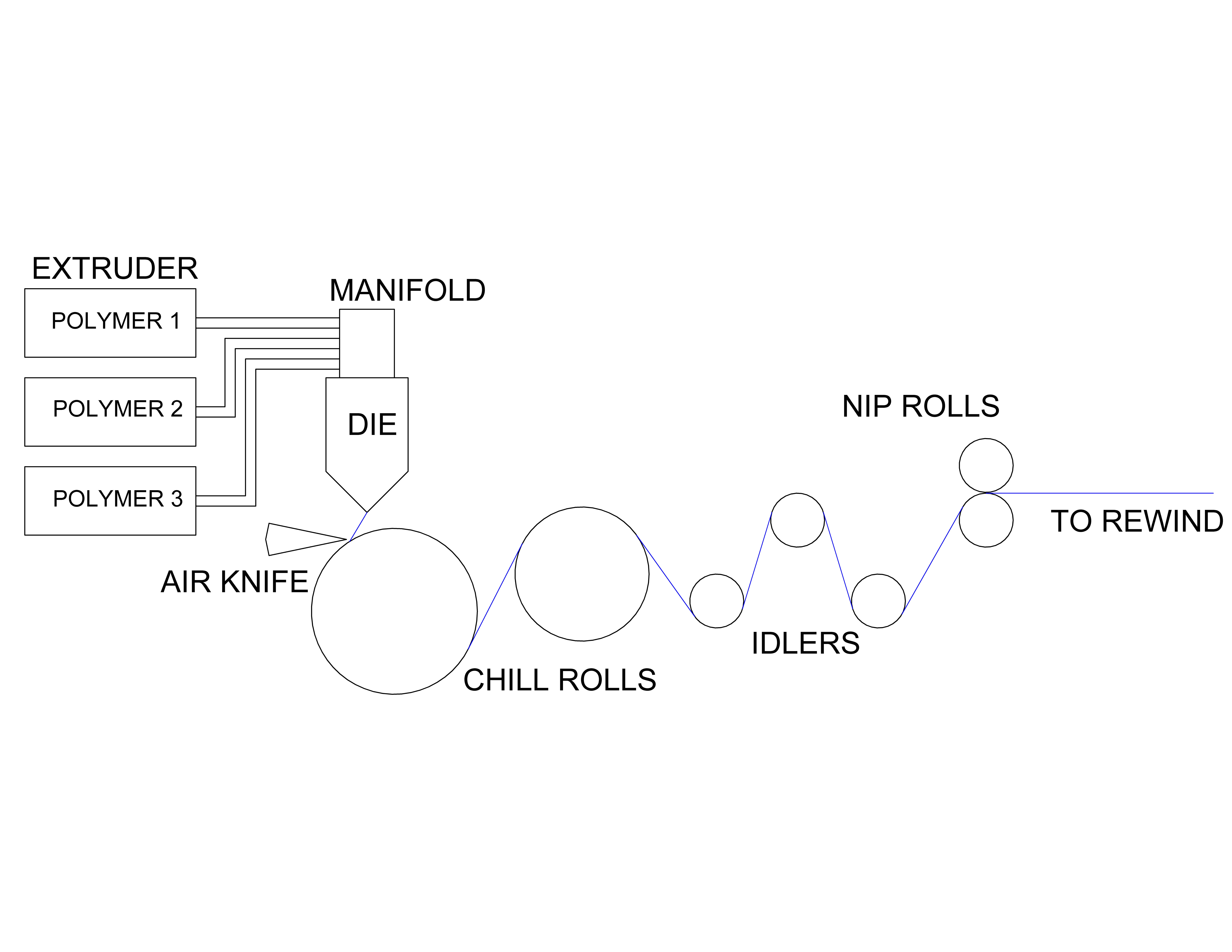
COMING SOON
Melt Blown Polypropylene Filter Media Extrusion Process
Melt blown polypropylene filter media is used as an absorbent dressing material in medical textiles. Due to the high filtration efficiency of melt blown polypropylene non woven webs, they are widely used in air filtration applications, protein purification (isolating protein/s from tissues, cells, or organisms), and DNA extraction, RNA extraction.
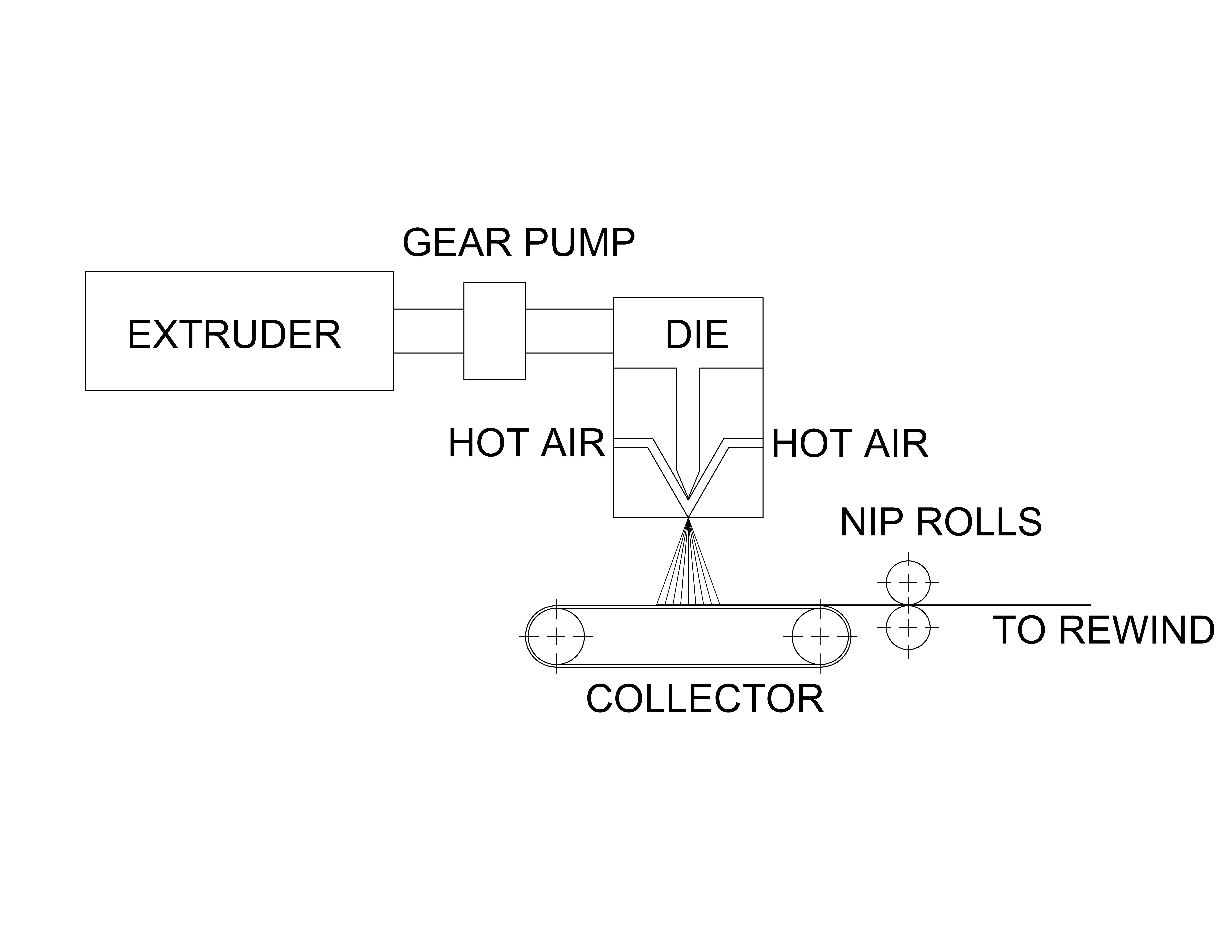
Explore our converting capabilities:
Explore our converting solutions
Learn how we’ve helped our customers with a wide range of Converting solutions
PLITEK® is an ISO 9001:2015 and ISO 13485:2016 certified global converting leader.