Rotary vs. Flatbed Die Cutting
At the early stage of a new precision die cutting project, it is essential to determine the process best suited for your application. How do you decide? Let’s evaluate rotary vs. flatbed die cutting.
Rotary die cutting is the process of cutting or perforating a requested shape from a flexible material with rotary machines. During this process, a continuous web of flexible material is fed through the rotary press through the nip rollers to a cylindrical die that cuts, perforates, or creases the film. This cutting method is synonymous with rapid speeds, acute accuracy, and tight tolerance thanks to rotary machinery’s technical sophistication. These qualities demonstrate rotary die cutting’s ability to handle complex projects that need a fast turnaround. Multiple material lamination, slitting, sheeting, and in-line cutting registration are some of these project types.
In contrast, flatbed die cutting is the reciprocating vertical stamping process using a die with blades that are bent and press-fit into a laser cut die board. Die boards can be made of a variety of substrates including wood, phenolic, polycarbonate, and other materials depending on the application. Some additional benefits include low tooling costs, shorter tooling lead time, and ability to cut thick materials.
The ability to cut thick materials is what sets this method apart from rotary die cutting which is primarily used on thin and flexible materials. Thick materials with the ability to cut with flatbed die cutting process are films, foams, and adhesives. These parts can be provided in roll, sheet, or piece form with a variety of peel tab options.
Which one is best for your project? The final decision lies within the details of your project – materials, size, precision of cuts, etc.
Things to Consider:
Materials:
– Thin and Flexible Materials – Rotary Die Cutting
– Thick Materials and Harder Materials – Flatbed Die Cutting
Speed:
– Higher speed – Rotary
– Lower speed – Flatbed
Precision of Cuts:
– Intricate Cut – Rotary
– General Cuts – Flatbed
Want to learn more about which method fits your project needs? PLITEK® offers both options. Our team is ready to aid you with your project needs – reach out to us.
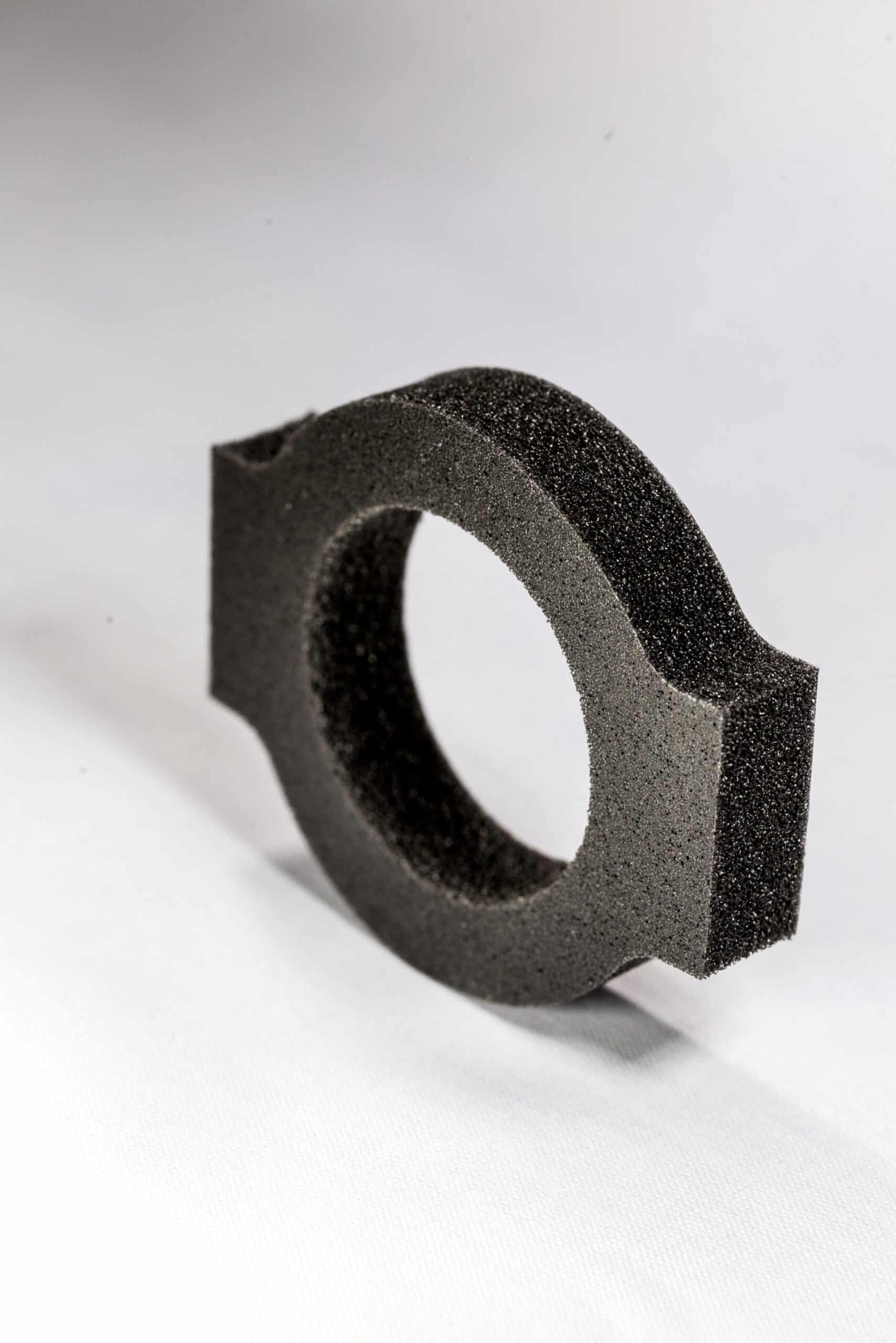
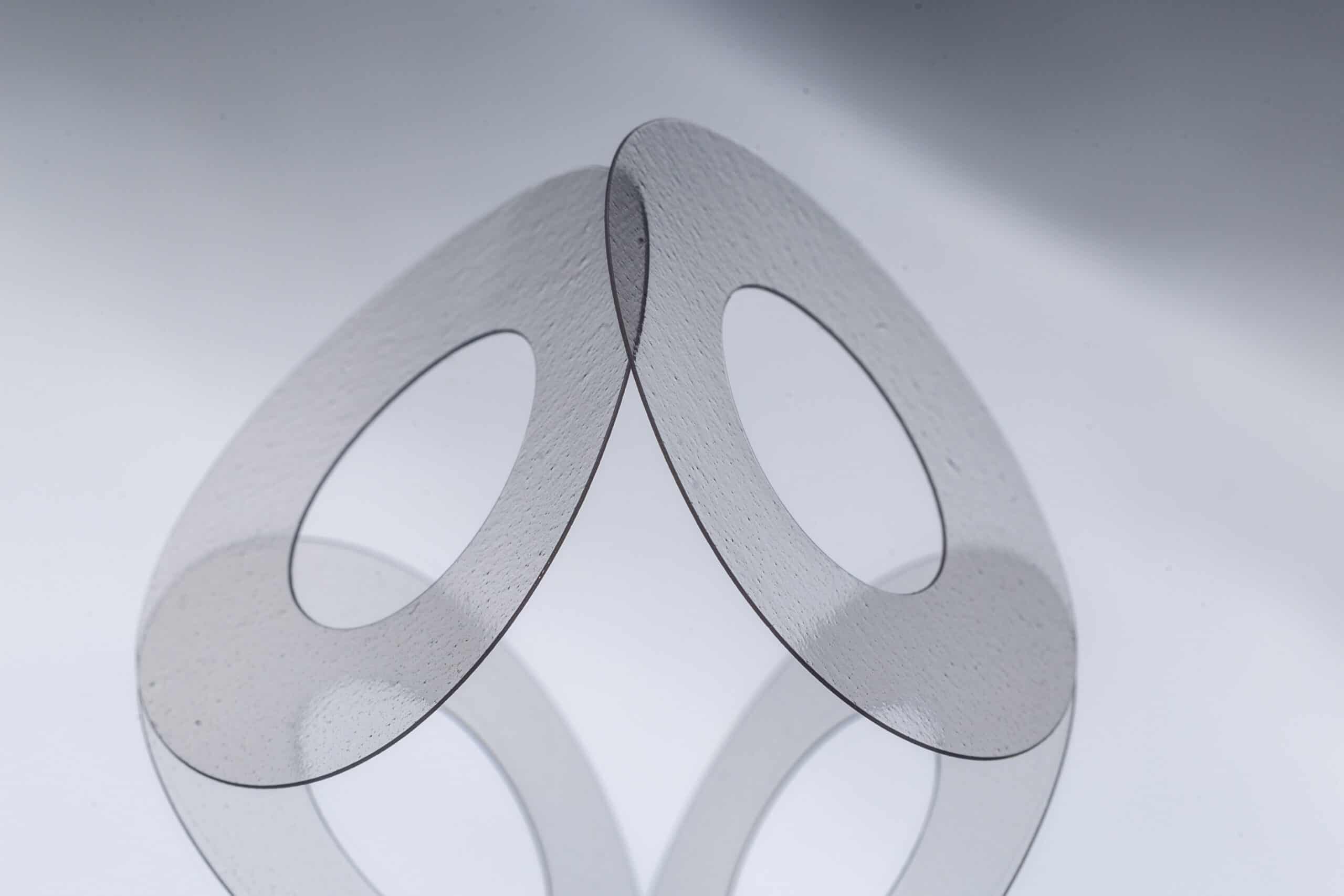
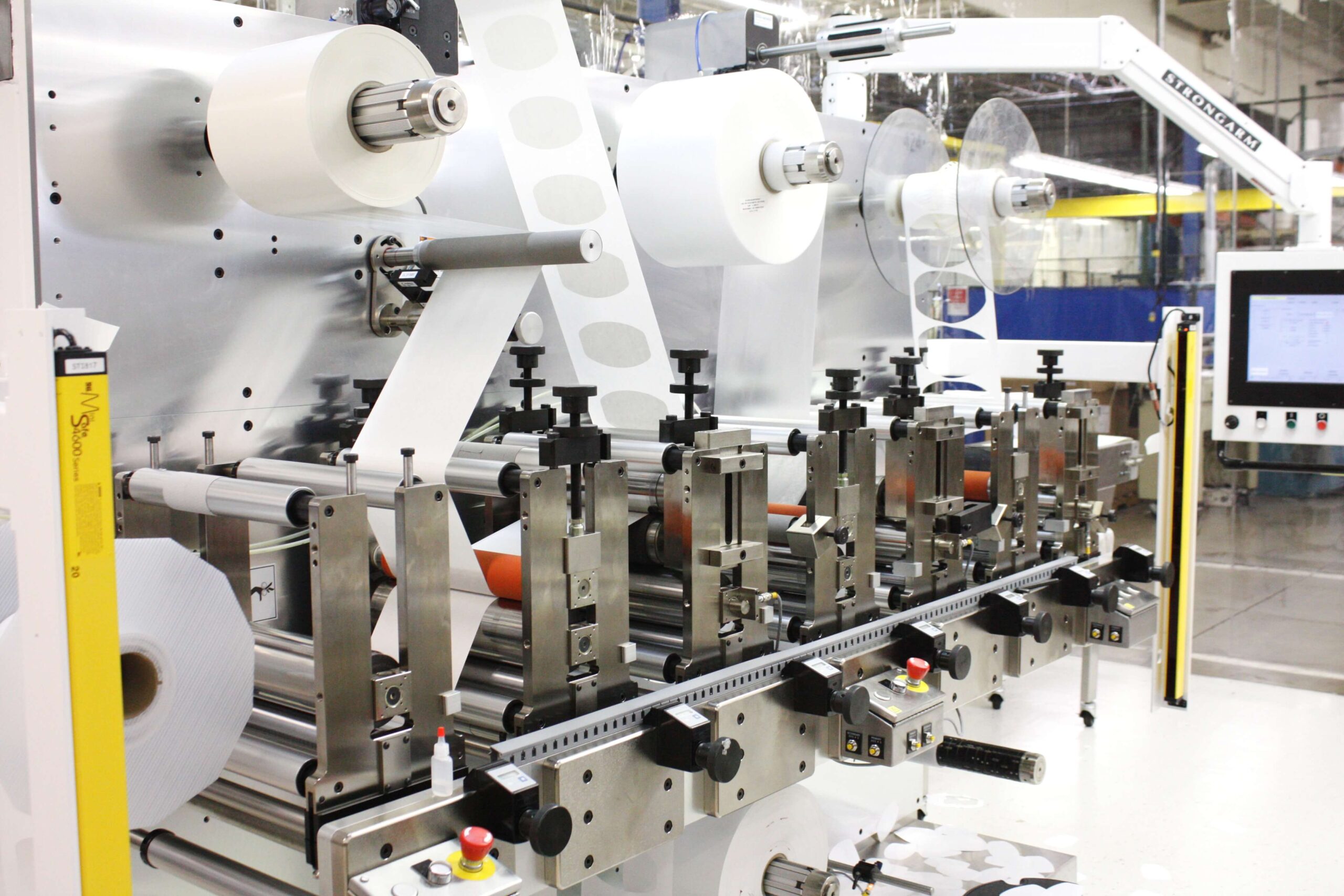
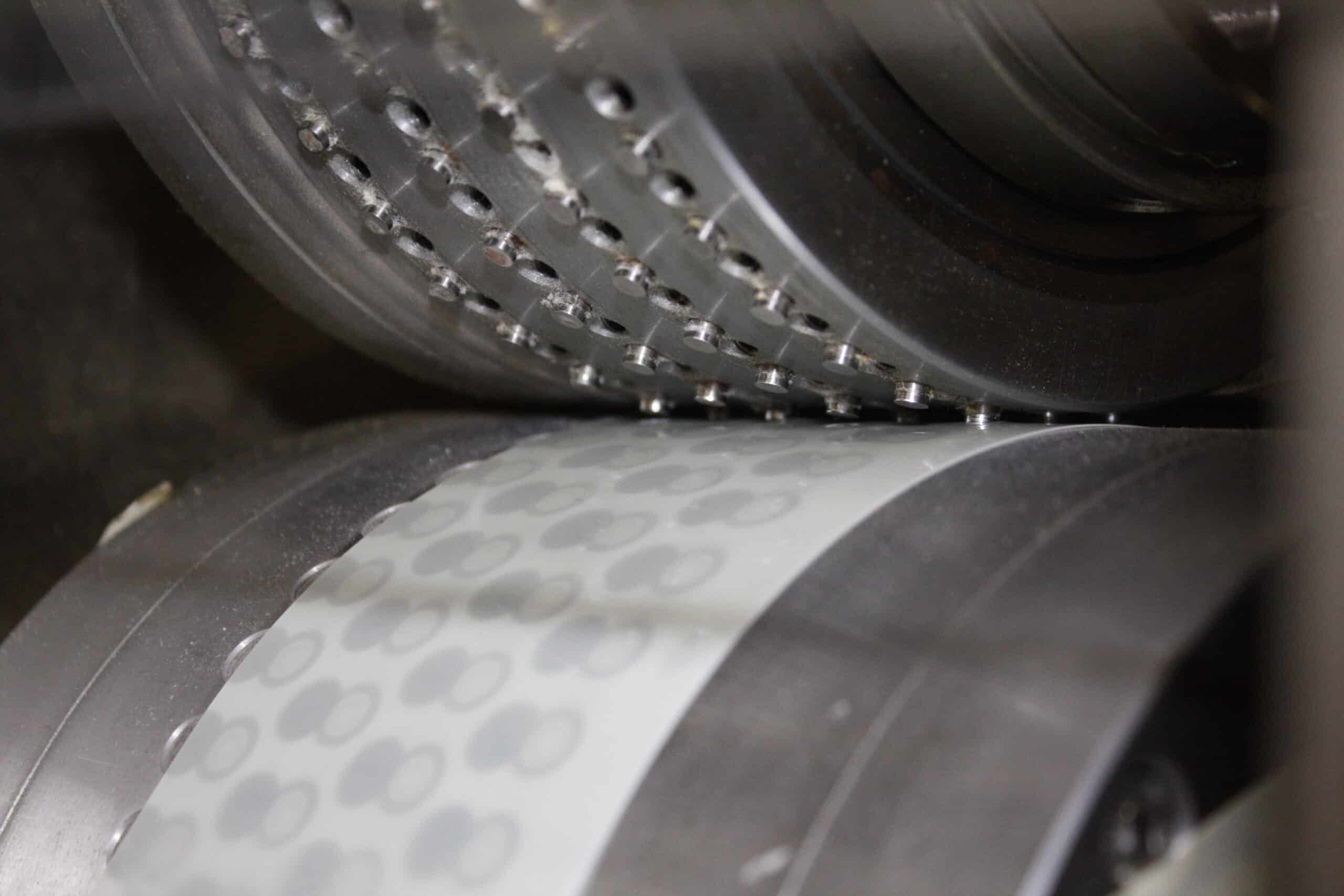
PLITEK® is an ISO 9001:2015 and ISO 13485:2016 certified global converting leader.