Surface protection films play an important role across a range of industries preserving quality, functionality, and appearance at different stages—from production and transport to installation and long-term use. These thin film layers not only shield surfaces from scratches, abrasions, dust, and chemical damage but also help maintain the pristine condition of materials in demanding environments. Surface protection films are used temporarily as safeguards during manufacturing, shipping, or installation, but can, in some cases, serve as a permanent protective layers. Surface protection films are often used in applications such as medical devices, consumer electronics, automotive components, and others.
PLITEK® manufactures surface protective tapes and films for various applications. Our surface protection products are available in roll or piece form. With our extensive manufacturing expertise and materials knowledge, we can help select the most suitable material for the application.
PLITEK® has over 50 years of experience die cutting surface protection films for a range of industries. Our innovative manufacturing capabilities, proven expertise, consistency, and strict quality standards keeps PLITEK® a continual leader in manufacturing of die cut components and converted materials for industries requiring quality surface protection films.
We also offer product development support, manufacture a small prototype quantity required for product validation, and produce high volume component quantities.
PLITEK® offers die cutting services in state-of-the-art ISO Class 8 (100,000) clean rooms available for every step of the manufacturing process. In addition, materials and parts can be produced, inspected and packaged in the clean rooms to ensure parts are free of foreign particles and contamination that could impact product integrity.
Surface Protection Films Applications:
Surface Protection for Medical Devices
Touchscreen and Display Protection:
Medical monitors, infusion pumps, and diagnostic tablets use ultra-clear, anti-glare films. These films protect sensitive touchscreens from scratches, smudges, and chemical exposure, ensuring consistent performance and easy disinfection.
Optical Component Safeguarding:
Devices such as endoscopes, surgical microscopes, and otoscopes require films that preserve optical clarity. Protective films on lenses and sensor covers prevent scratches and contaminants while maintaining high-quality image transmission, which is critical for accurate diagnostics and surgeries.
Surgical Instrument Packaging:
During transportation and storage, surgical instruments are often encased in temporary protective films. These films shield delicate surfaces from abrasion and contamination, ensuring that instruments arrive sterile and in optimal condition for use.
Implantable Device Manufacturing:
For devices like pacemakers or orthopedic implants, protective films are applied during manufacturing to protect surface finishes from contaminants or scratches. These films are removed just before final sterilization, ensuring the implant’s surface remains pristine.
Laboratory Equipment Preservation:
In clinical laboratories, high-precision instruments such as spectrophotometers and microscopes use protective films to guard against dust, chemical exposure, and minor abrasions. This helps maintain the accuracy and longevity of sensitive measurement equipment.
Surface Protection for Medical Devices for Consumer Electronics
Screen Protection: Films are used on smartphones, tablets, laptops, and monitors to prevent scratches and smudges.
Component Safeguarding: They protect sensitive components during assembly and shipping, ensuring displays and finishes remain pristine.
Surface Protection for Medical Devices for Automotive Industry
- Exterior Protection: Applied to car bodies, these films help shield against minor abrasions, stone chips, and environmental contaminants.
- Interior Trim: Films can also protect dashboards, door panels, and other interior surfaces from wear and tear during production and transport.
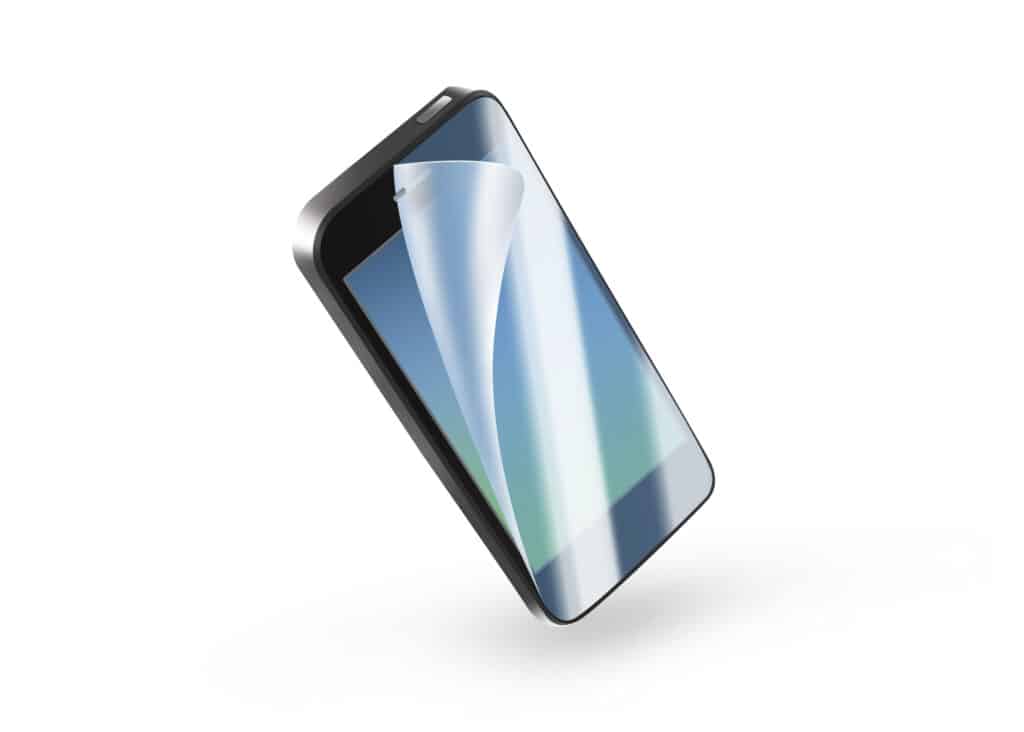
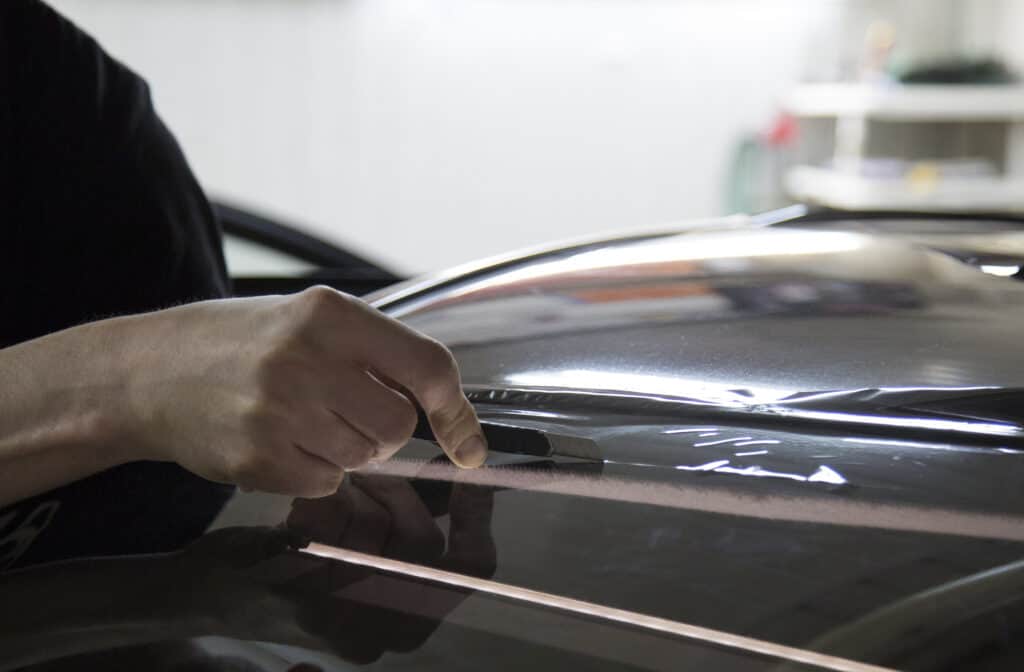
PLITEK® is an ISO 9001:2015 and ISO 13485:2016 certified global converting leader.